What are violin strings made out of? Gut, really?
Many different materials are used to make violin or orchestra string instrument strings. The best way to understand what they are made out of is to look at the history of string making. The progress in science as in craftsmanship is regular and logical and explains by itself why certain material has been developed and chosen over another one.
Date | String material | characteristics |
---|---|---|
1500 BC | Plain sheep gut strings | Warm rich and historic tone |
1700 | Wound gut core strings | Warm tone with greater stability |
1900 | Steel core strings | Brilliance and volume, best for highest pitched strings |
1940 | Stranded core strings | Brilliance and volume |
1970 | Nylon core strings | Warm tone with a steel core string like stability |
1990 | Advanced synthetic strings | Rich gut strings like overtones with great sturdiness and bow response, low break-in time |
So, how have we come from plain gut strings to advanced synthetic core strings, and what are the advantages of new strings? Let’s see what to consider to understand what violin strings are made out of.
Why are different materials used to make strings?
Luthiers, string makers, and violinists have something in common: a passion to get the perfect sound, the perfect tone. But there are many different circumstances: soft music, chamber music, baroque orchestras, big halls, romantic repertoire: so if a perfect doesn’t exist, versatility and diversity are essential in tone production. That is why, naturally, string makers have experienced many different materials to accompany the violinists in their never-ending quest. So different materials could eventually move away from the traditional gut strings to new sounds and territories.
Different tonal characters and diversity have been reached, different instruments could get their matching type of strings.
Different types of concerts were matched with broad dynamic ranges. The greatest soloists could benefit from an incredible bow response and left-hand playability.
Different tunings, different violin setups could be complemented with different string tensions. Lastly, the ever-going battle against wolf tones, buzzing, or whistling strings could find a happy end.
Traditionally, violin strings were made out of sheep gut
Plain gut core strings
Traditionally, string instrument strings were made out of natural sheep gut, made by hand.
It was the original material used in all string instruments and was first seen on a Lute dating to 1500 before Christ in Egypt.
Plain gut strings are made out of stretched sheep intestine and give a particularly rich and warm tone. It takes a long time to stretch and cure a gut string, and this process is most of the time made by hand.
Gut strings are often used by Baroque musicians for the warm sound they give, and because they sound particularly well with the lower tension of the baroque way of setting up the instrument. If you read my article on how to tune a violin, I have detailed how the A was different at 436 Hz during the baroque era, and how it gave a lower and some say reacher tone.
They have a rich a great detailed tone but suffer greatly from differences in temperature and humidity and are prone to over-stretching. This is why gut strings should be loosened when you travel by air (the atmosphere becomes dry at the altitude, and the strings can break). Gut strings have a long break-in period and bad tuning stability. That is why other materials have been developed to overcome these shortcomings.
Winded gut core strings
The winding added on today’s gut strings can be traced back to the time of Stradivari in the 18th century. The winding itself uses metals that I have detailed down below, in the synthetic core strings paragraph.
Metal core strings
They were used for the higher strings in conjunction with gut strings for the lower strings. David Oistrakh used wound gut strings for G and D and metal strings for A and E.
Solid steel core strings
They are called plain strings.
They have a solid steel core and were first invented at the beginning of the 20th century. It was the Russian school of the violin that pioneered the use of metallic strings (as opposed to gut strings) for the E and even sometimes for the A string. Heifetz used an E string which gave him more volume, playability, and brilliance in the higher-pitched notes of the repertoire. In great concert halls, his sound was just legendary. The smooth, supple, and rich sound of the lower-pitched strings wasn’t enough to come through with a gut E. But, since the first steel strings, many different materials have been tried and used to make a metallic string.
Solid steel core strings have far better tuning stability, allow more bow pressure and tension. They have accompanied the transition to a higher-pitched A, towards 440 Hz, up to 444 Hz as the Russian orchestras used to play.
Around the steel core, there can be up to six layers of windings. The manufacturing process to make steel core strings is easier. They are also cheaper and sturdy, which makes them the perfect match for beginners and fiddlers out on the road.
Stranded steel core strings
Developed during the second half of the 20th century, stranded steel core strings are also called rope core strings. They responded to the need for new sounds, flexibility, and response that could offer regular steel core strings.
Depending on the number of strands, the tension, bow response, tone, and color are different. Brands have experimented a lot in that area. Depending on the quality, stranded strings can be played by beginners to professionals.
What material is used to make the core of a synthetic core string?
The core material is said to be synthetic, as opposed to natural sheep gut core. But under this generic term, several synthetics can be used, such as:
- polyester of different kinds of polyaryletherketones,
- polyamides: for example perlon or nylon.
But the core material can also be made out of:
- chromium steel;
- carbon steel;
- stranded steel.
As we have seen above.
The core materials of the strings are responsible for the string tension and provide tonal flavor. The key characteristic here is the mass per length ratio.
So the material is chosen considering the pitch of the string: the higher the pitch, the less mass it should have.
This is why violin E strings and viola A string does not have a winding, especially a silver wound.
Nylon core strings
Nylon core strings were the first breakthrough as they eventually gave the long-awaited tone close to gut strings with great playability, tuning stability, and bow response. As a result, they are still often used today and played both by beginners and professionals. They are not prone to differences in length, tone, or tension in variable weather conditions.
Advanced synthetic core strings
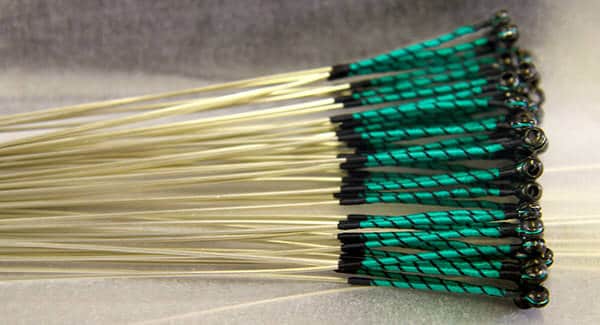
As science never stops, in the 1990s a new type of synthetic strings was created, even better than nylon. Strings have benefited from the research in the space industry where materials immune to heat and pressure have been developed. If strings can give the best of both worlds, it is advanced synthetic core strings:
- they have a tone with a warmth and richness closest to the best gut strings;
- like steel core strings, they have great tuning stability, bow response time, tension, and low break-in time.
They are a bit more expensive, not as much as gut strings, but last long. Beginners to professionals use them.
What types of metal are used to make violin, viola, cello, or bass strings?
For the G, D, and sometimes A strings, a nylon core is winded with metal wires
The synthetic core, made out of nylon, has been invented to replace the sheep gut core. Around this synthetic core, there is a metal winding to protect and enhance it. The winding is either flat or round: with a flat winding your finger doesn’t feel any texture, the string is perfectly smooth. There is a perfect left-hand sliding feel.
The winding can be made out of :
- aluminum winding needs a higher diameter, but gives a great bow response, a brilliant sound, but has average corrosion resistance.
- silver winding accommodates with a smaller diameter, but gives a string with average characteristics, whether sound wise or play wise; the corrosion resistance is better than with aluminum winding though.
- Chromium still winding needs greater diameter; the bow response is somehow lacking. The sliding feel of the left hand is excellent. The sound is darker and less brilliant. Volume and resistance to corrosion are excellent.
The metal winding can be seen as a way to customize the tone of the raw string. Different types of sounds can be experimented with by changing the metal used in the winding.
- Silver and tungsten are heavy and dense. They are used to make strings with warm sound and great projection. Silver is used to making lower strings of the violin or viola as the tone is warm;
- Aluminum and nickel are lighter and chosen to make brighter and more brilliant tones;
- Titanium is often used in an alloy with silver. As it is a light metal it gives warm strings, which are perfect for viola or cello;
- Gold: a heavy metal with warm and brilliant sound, often used to coat E strings for violin. Higher-end E strings are designed not to whistle and are often made with gold.
- Tin can also be used to plate steel core strings to achieve a different tone.